Commercial Refrigeration Repair is important for businesses that depend on refrigeration, like grocery stores, restaurants and food processing facilities. Timely repairs avoid inventory loss, keep food safe and reduce energy costs.
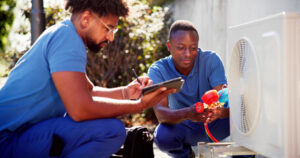
Start with basic troubleshooting. Make sure the unit is plugged in and getting power. Then check the thermostat settings and evaporator fan. Clean coils prevent overheating and increase efficiency. Connect with Commercial Refrigeration Repair Near Me for reliable help.
1. Thermostat
Thermostats are a vital part of commercial refrigeration systems, as they help to regulate the temperature within the refrigerator. However, they can also be a source of trouble if they are not working correctly. This is why it is important to take some time to understand how thermostats work and what steps you can take to prevent problems.
A common problem with refrigerators is that they do not maintain the proper temperature. This can be caused by a malfunctioning thermostat, an issue with the compressor, or a broken condenser coil. In order to determine the cause, it is a good idea to turn off the unit and check the settings. Once you have done this, it is important to see if the unit can maintain a consistent temperature. If not, it is likely that the thermostat needs to be replaced.
Another sign that the thermostat is the culprit is if the fridge cycles on and off frequently. This can be a sign that the unit is overworking, and it can lead to higher energy costs. In addition, it can also lead to food spoilage. To avoid this, it is a good idea to check the drain pan and tubing regularly for food particles or dirt.
A professional technician can easily diagnose the cause of the problem and provide a solution. This can include replacing parts, repairing leaks, or changing the system settings to improve efficiency. In addition, a professional can conduct regular maintenance to keep the refrigerator running smoothly. This can help to extend the life of the system and save money on repair costs in the long run.
2. Compressor
The compressor is the heart of a refrigeration system. It takes air from the atmosphere, pumps it through a series of stages and pumps it back out to the atmosphere at higher pressures.
There are a variety of types and uses for compressors. They are used in industries that use refrigeration, waste disposal and raw material processing systems. It is important to understand more about compressors and their functions, types and workings.
A commercial refrigerator requires regular maintenance to keep it in good condition. A professional technician can help with this and also perform a thorough inspection to spot potential problems. They can identify issues that aren’t readily apparent to the untrained eye and fix them before they become major problems that require costly repairs or even replacement of the unit.
Some of the signs that a commercial fridge is in need of service are moisture and ice build-up in the evaporator or condenser, water leaks (from worn seals or clogged drains), temperature leaks (from door gaskets that aren’t sealing properly or cooling fans that are obstructed), and electrical problems (from overloaded circuits). A rattling sound can indicate that the evaporator fan motor screws are loose, while a screeching sound suggests that the fan belt needs replacing.
If these problems are not addressed quickly, they can result in a loss of product that could cost a business a lot of money. To avoid this, it is recommended to call in a professional refrigeration repair company to regularly perform maintenance and repairs on the equipment. They have specialized tools and LEED Certification Solutions knowledge to do the job safely and efficiently. They can also give valuable advice on preventative maintenance to avoid future problems.
3. Door
A commercial refrigerator needs a solid door to keep cool air inside and warm air out, as well as help with regulating temperature. However, swinging doors can put a lot of stress on hinges and closing mechanisms, leading to failure over time.
Likewise, a cracked or broken door gasket does not seal properly, letting cool air escape and warming food up prematurely. This negatively impacts food preservation and safety and can lead to expensive repairs or even a health code violation.
Routine cleaning and maintenance is a good way to prevent problems with your walk-in refrigeration unit, including the door. Regularly wipe down the bottom interior and shelving to remove condensation, dirt, and food particles. Clean door gaskets and check for cracks or tears. And don’t forget to re-lubricate hinges regularly, too. In addition, it’s a good idea to run a dollar bill test once per month: try putting a bill in the frame with some sticking out and shutting the door. If you can pull the bill out easily, your door seals are in need of repair.
4. Drain pan
The drain pan is a simple yet important component of the refrigeration unit. Its purpose is to capture any incidental water leaks that may occur from the compressor or evaporator coil, preventing them from reaching other components and damaging them. Unfortunately, the drain pan can also clog and overflow, due to poor maintenance and lack of routine inspections. When this happens, the resulting damage can lead to costly repairs and lost business.
Drain line blockages can cause the refrigeration system to work harder than necessary, which ultimately leads to reduced efficiency and higher energy bills. Additionally, stagnant water can become a breeding ground for mold and bacteria, which in turn can negatively impact indoor air quality.
It is important to check the drain pan and tubing regularly for signs of blockages, such as a buildup of dirt or food particles. A simple visual inspection can often reveal these issues. Using a soft brush, it is possible to remove any debris that has accumulated in the pan or tubing. Flushing the lines with warm water can help break down more stubborn clogs. For more serious blockages, commercial drain line cleaners can be highly effective at breaking down fats and oils, which are commonly found in the refrigeration unit’s drain lines.
By following the tips in this article, it is possible to improve the longevity of your refrigeration unit and prevent costly and inconvenient problems from occurring. Regular maintenance and routine inspections can significantly reduce the risk of unexpected breakdowns and keep your business running smoothly. The most important thing to remember is that prevention is the key! This means being vigilant and performing routine maintenance on your commercial refrigeration unit.
5. Tubing
If your refrigeration system consists of copper tubing, it’s important to keep an eye on its condition. Despite its superior thermal efficiency, copper is susceptible to corrosion from acidic substances. This may cause the tubing to leak, or even rupture. To minimize damage, it’s a good idea to use a professional tube bender when making sharp bends. This tool helps prevent collapsing the tubing and allows for a clean connection without exposing exposed metals. It is also advisable to avoid direct contact between dissimilar metals, as this can cause galvanic corrosion.
Another common issue with refrigeration piping is blockages, which can result in a reduced cooling capacity and higher energy consumption. This is often caused by improper sizing and installation during initial installation, as well as by a lack of regular maintenance. In most cases, these problems can be easily fixed by a qualified technician.
Unusual noises, such as chattering or clicking, are also a clear sign that something is wrong with the refrigerator. It’s always a good idea to check that the power supply is fully off by flipping the circuit breaker, and to make sure all fuses are not blown using a voltage tester. Before attempting any work on electrical components, be sure to de-energize the unit and wear rubber gloves for safety.
While commercial refrigeration repair costs can be expensive, routine maintenance can reduce the risk of unforeseen problems. This can help to minimize inventory loss, improve the cooling efficiency of the unit and save on energy bills. With these tips in mind, it is important to budget for expected repairs. It’s also a good idea to get familiar with your warranty terms so that you know exactly what’s covered and what isn’t.